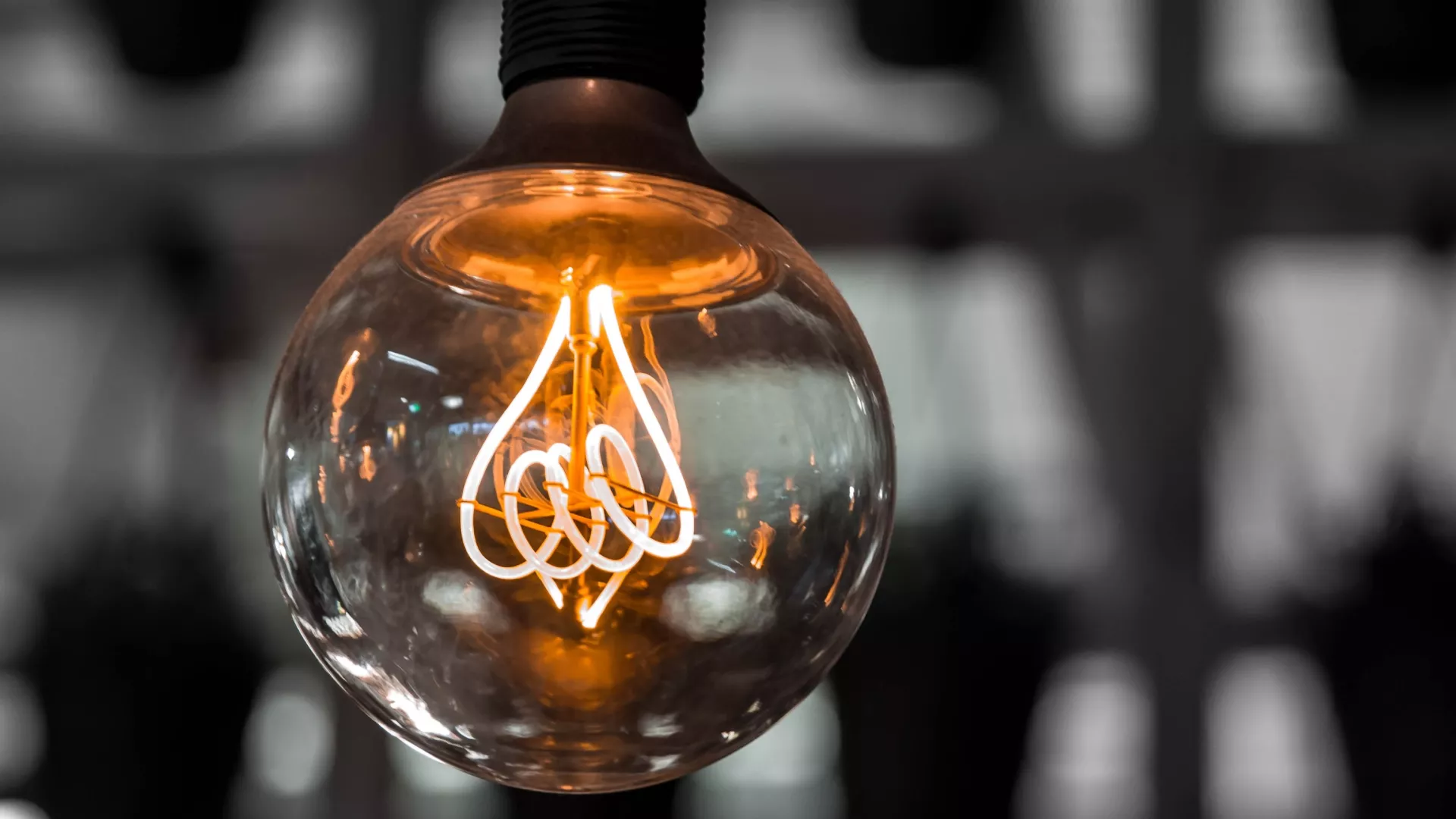
CAPAE
1. What are the objectives of the project?
The main objective of the project is to research the implementation of active noise control systems (pressure waves) of the acoustic-structural type in the control rooms of existing hydroelectric power plants. To achieve this, a prototype will be designed and developed for the control room of a hydroelectric plant in EDP Spain, specifically the La Florida plant located in the Asturian municipality of Tineo.
This main objective can be broken down into the following goals:
Develop technology and new knowledge related to the performance of active noise control systems in industrial environments, such as the control rooms in turbine buildings.
Explore the possibility of extending the proposed system to several plants, and its various potential uses and functionalities (noise control, but also predictive control of anomalies when the signal patterns undergo significant changes).
Develop a full-scale experimental model at La Florida Hydroelectric Plant, to directly investigate the system's performance in the field.
Improve the comfort of workers in the control room at La Florida Hydroelectric Plant.
This project, in which Acoustic Engineering 3 and EDP participated, was financed by the Government of the Principality of Asturias through IDEPA and the Science, Technology, and Innovation Plan (PCTI) 2013-2017, as well as by the European Union through the European Regional Development Fund (ERDF).
2. What tasks have been performed?
To achieve the aforementioned objectives, a work plan was set up from early September 2017 to early August 2019, which can be summarized as follows:
Multiple working meetings of the project team (EDP, IA3, and collaborating companies).
Preparation of technical and functional specifications for the system.
Measurement of sound and vibration conditions at La Florida Hydroelectric Plant.
Specific modeling of the surfaces to be intervened on to reproduce their dynamic-structural behavior.
Testing protocols and trials, both structural and control, in the laboratory.
Testing and deployment of the system at La Florida Hydroelectric Plant.
3. What were the stages of the project?
The main phases completed in the project were:
Preparation of technical and functional specifications, as well as the cost structure of the product-process to be developed.
Development of numerical models in the ANSYS environment (acoustic module) and simulation of the fluid-structure interaction (coupled fields).
Development of the system and laboratory-level testing.
Construction and assembly of the experimental model in the field, instrumentation of the model, and monitoring and follow-up of results.
4. What results have been obtained?
The developed system consists of three main subsystems:
Receiver subsystem: A sensor capable of measuring accelerations (accelerometers).
Control subsystem: A microcontroller responsible for the system’s operation logic.
Actuator subsystem: A device capable of emitting a vibration in the propagation medium. It consists of an amplification stage and actuators.
To characterize the existing sound level, noise recordings were taken inside and outside the control room, and vibrations were measured at various points of the glazing, with different operating combinations of the hydraulic power plant's generator units.
4.1 Modeling
To simulate the dynamic-structural behavior of the glass partition under study, a numerical analysis of the system was performed using a 3D model in the ANSYS-MECHANICAL environment. This was done to reproduce its vibration modes and natural frequencies. The modeling helped define the sensor and actuator placement strategy.
4.2 Laboratory Tests
First, various tests were conducted to verify the operation of the active noise control system using an initially horizontally positioned glass partition supported by four points. This prototype was 1x1.4 meters, simulating a panel of the glazing.
A forced vibration was used to excite the glass, and after performing the initial adjustments and several tests, it was confirmed that when the active noise control system was activated, the amplitude of the signal was reduced.
After confirming the effectiveness of the system, its operation was tested on a second prototype. This prototype simulates an enclosed space or cabin, enabling the study of airborne and structural sound transmission from a source placed in the center of the cabin. This helps approximate acoustic conditions inside a room, such as wave reflections and structural transmission.
Two types of tests were performed on this second prototype: acoustic tests and vibration tests.
Acoustic tests: A semi-dodecahedron source emitting a pure tone of 93 Hz was placed inside the test cabin, and an acoustic measurement was taken 0.5 meters from the cabin. This allowed the assessment of the sound level outside the cabin when the active noise control system was not operating. The experimental system achieved an attenuation of 11 dB in the third-octave frequency band of the excitation frequency when the active noise control system was operating.
Non-acoustic tests: Vibration measurements were taken using accelerometers. A semi-dodecahedron source emitting a pure tone of 93 Hz was placed inside the test cabin, and vibration measurements were taken. This allowed the assessment of the vibration level on the glass surface of the cabin, both with the active noise control system on and off. Notably, the vibration reduction reached approximately 80% on the experimental model's panel with the active noise control system operating.
4.2 Field Implementation
After performing similar tests as those conducted in the laboratory, and observing the field partition, it was necessary to analyze the transmission of mechanical waves (vibrations) generated out of phase by the actuator of the active noise control system. The arrangement of the panels, fixed to an aluminum frame, could affect the system's effectiveness.
Simultaneously, sound level measurements were made in the turbine room and inside the control cabin, with the active noise control system activated and deactivated. It was verified that the sound level was reduced by at least 2 dBA, and nearly 5 dB in certain frequencies.
In conclusion, it was found that the system achieved considerable vibration attenuation on the panels where it was applied. However, the discontinuity introduced by the frame disrupted the out-of-phase cancellation produced by the active noise control system, preventing the attenuation levels achieved in the laboratory with a continuous panel from being reached.
On the other hand, it is believed that the system can be improved to operate over a broader frequency range. By reducing vibrations over a wider range of frequencies, the system's efficiency can be increased.
Project funded by